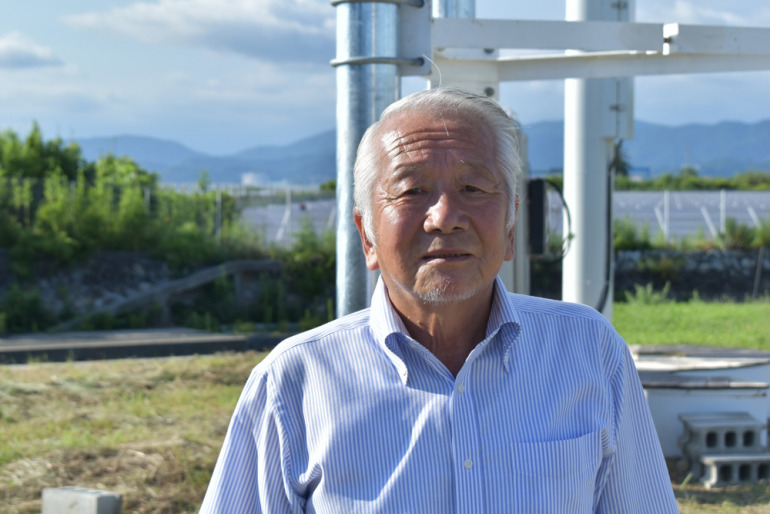
地球環境の保全に配慮し、未来の子供たちの利益を損なわない、持続可能な社会発展にコミットする製品や企業を紹介するシリーズ、「サステイナブルな企業のリアル」。
今回は風車のお話である。石油由来のエネルギーに代わるものとして、風力発電は再生可能エネルギーの代名詞であることは言うまでもない。
今回紹介するのは(株)グローバルエナジー 代表取締役鈴木政彦さん(70)。静岡県浜松市にある会社で、従業員は8名。すべて技術者である。静岡県浜松市出身の鈴木さんは、ニューベルシオンという小型風車を開発。ニューベルシオンの羽根は、従来の風車の羽根の長さの半分以下で、倍以上の出力を得られる。風力発電の風車に付きものとされた低周波の音もまったくしない。再生可能エネルギーの飛躍的な前進に、大きく貢献する発明の可能性があるのだ。
「結果はどうなんだ」ということ。
鈴木政彦は勉強が嫌いだった。地元の高校を卒業後、職をいくつか替え、解体屋で入手した4tトラックを自分で修理し、運送業を手掛けたこともある。浄化槽の製造メーカーに勤める知人から、部品作りを持ちかけられて会社を興したのは20代前半。それが後年、画期的な風車の開発へと繋がっていく。
「僕が常に注目しているのは、“結果はどうなんだ”ということ。過程がどうであれ、得られる結果がすべてではないかということです」
仕事はFRP(繊維強化プラスチック)といって、ガラス繊維と樹脂と硬化剤を塗ってローラーで中の気泡を抜き、固まったら型から抜き浄化槽の枠を納品する。当初は教えられた通りやったが、樹脂とガラス繊維を同時に吹き付ける方法を考案。当時珍しかったコンピューターを使い、吹き付けるポンプの往復運動を計算して、最適な塗布と焼き具合を作業者に指示する装置を開発。下請け企業の中で売り上げがトップになった。その後、FRPの技術が認められ、大手企業の下請けとして茨城や栃木に工場を持つ。40代後半には商売上のトラブルで倒産の危機に見舞われたこともあったが、それを乗り越えた2000年頃の話である。
“科学”の常識とは、真逆の非常識
「世話になった隣町の町長が、レタスを人工で生産する野菜工場を立ち上げたんです。
太陽光の代わりにLEDを使ったが、LEDの電気代がかさむ。そこで風車を使い風力発電で電気を自分で賄えないか、そんな相談されたんです」
「面白い」と即答した鈴木は、紹介された風車の権威である大学の先生のもとに通い、風車について一から勉強をはじめる。
「ところが教わった通りにやっても、いい結果が出ない。納得のいくものができなかったんですよ」
例えば風力発電の風車は、根本が太く先端が細い。だがテコの原理で考えた時、軸から一番遠いところを太くして風を受けたほうが、強い回転力を得られるのではないか。
「僕が気になったのは風車の音です」
――風力発電の低周波音は騒音問題になっていますが、風切音を取り除くことができるのですか。
「例えば釣り竿でもゴルフクラブでも、細いものを振ると後ろで乱流が起こる。それが風切音の原因です。ところが板を振っても音は出ない。つまり板は乱流を起こさない」
先端の翼面積を板のように広くする。それにより風切音は出にくくなり、より風を受けられて、強い回転力を得られる。
――でも効率を考え、抵抗が少ないものを設計する、それが科学の常識でだと、シロウト目にもそんな認識があります。ところが鈴木さんのやり方は、わざわざ抵抗を増やしているように見えます。
「抵抗を増やすのではなく、抵抗を利用するのです」
鈴木は、ベルシオンを発想した基本的な考え方の説明をはじめる。
抵抗をエネルギーとして利用している
「川魚の遡上を考えてみてください。川の水量が少なく、チョロチョロとしか流れがない段差は水の抵抗が弱い。でも魚は遡上できません。ところが流れが激しく水の抵抗が強い段差では、魚は軽々とジャンプして飛ぶように遡上していく。
一般的な科学の常識からいえば、抵抗が少ないほうが速く泳げる。それで言えば海の魚はヒラメやエイや、平べったい魚が速いはずだ。ところが高速で泳ぐマグロやカツオは、ずんぐりむっくりした形をしている。頭が大きくて体は太い、尻は尖っていて流線形です。速く泳げる魚は、人間が抵抗と考えている力をエネルギーとして利用している。高速で泳ぐ魚の形は、抵抗をエネルギーに変える最適な姿なんです」
抵抗をエネルギーとして使いたい、マグロやカツオの形を風車の羽根に生かすことはできないか――、鈴木の脳裏の中で次々とイメージが展開する。
暴風雨に遭遇、「早く壊れてくれ…」
「鈴木さん、風車の羽根は航空力学に基づいて設計されているんですよ。シロウトが介入する余地がない分野です」
大学で航空力学や翼理論を学んだ専門家からのそんな冷笑を、鈴木は数限りなく浴びせられてきた。
「だから、学者の先生が考えた理論的に正しい風車が、僕の作った風車の半分も力が出ないことを証明してやろうと」
彼は試作に没頭した。風車は垂直軸型風車とプロペラ型風車とがあるが、羽根の形、厚さ、長さ、力の出る要素は何なのか。3Dプリンターが普及する以前は、自分で切って削って試作品を製作し、風洞実験を含め垂直型約4000基、プロペラ型2000基以上、試作を試みた。
「当初は壊れない風車を目指しました。独自の理論で設計した風車の強度を徐々に高め、通常の試験運転では全く問題がない風車が完成したんです」
ベルシオンと名付ける、これまでにない羽根を用いた風車に喜んだのも束の間、ある日、試験運転中に暴風雨が襲来した。強烈な突風が吹き荒れ、制御が追い付かず発電機は焼け、ブレーキも真っ赤になったが、頑丈に作った風車を止めることができない。制御不能でブンブン回る風車を前に手の施しようがなかった。
早く壊れてくれ――、鈴木は思わず天を仰いだ。
限界を超えた時は壊れる。制御不能になった時に羽根が壊れ、他の装置に被害を及ぼさないことが大切だと、痛感される出来事だった。
だが、羽根が壊れて飛んでしまったら、二次災害を起こす危険性がある。壊れて飛んで行っても、羽根が二次災害を起こさない、安全な素材を使うことが絶対条件だ。
さて、その安全な素材は何だったのか。素材をクリアして、完成したベルシオンの特許専用権を大企業に十数億円で譲渡。さらにニューベルシオンへと進化する物語は、明日公開の後編で。
取材・文/根岸康雄
http://根岸康雄.yokohama