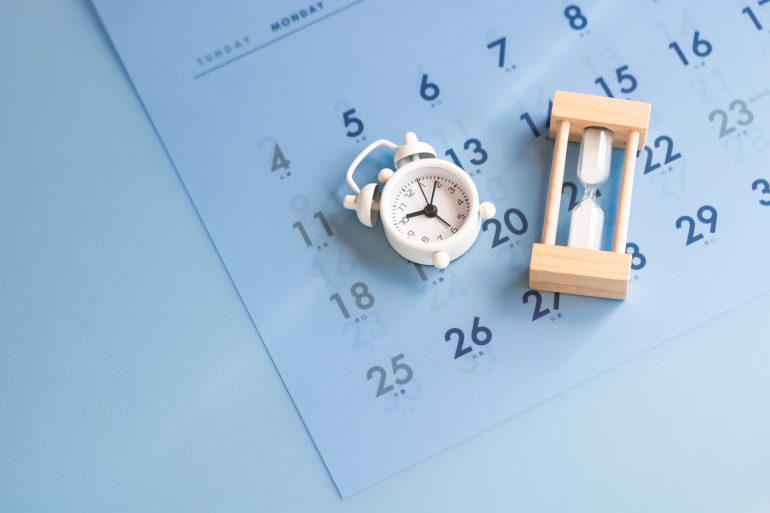
『リードタイム』は、企業の競争力や顧客の満足度に関わる重要な概念で、あらゆる業界で重要視されています。リードタイムの意味や種類、短縮するメリットを解説します。
目次
ビジネスでは、『リードタイム』という言葉がよく使われます。業務改善の指標としても用いられ、多くの企業はリードタイムの適正な短縮に努めています。言葉の意味を覚えて、ビジネスシーンで有効活用していきましょう。
リードタイムとは?
まずは基本的な概念や特徴、納期との関係性を確認しましょう。
■業務の効率化を図る上で重要な概念
リードタイム(Lead Time)とは、ある物事に着手してから終了するまでにかかる時間のことです。厳密には、リードタイムの始点と終点の設定によって、いくつかの種類に分かれます。
- 調達リードタイム:材料の仕入れから納入までの期間
- 生産リードタイム:生産を開始してから生産が完了するまでの期間
- 製造リードタイム:原材料投入から製品出荷までの期間
- 配送リードタイム:商品の発送から配達完了までの期間
リードタイムは、企業の業務プロセス全体を反映する重要な指標であり、効率化を図る上で重要です。
■納期との比較
『納期』は、『納入期限』を略したものです。製品・サービスを顧客に収めるまでの期限を指し、『〇月〇日』という具体的な期日で表されるのが一般的です。
リードタイムは開始から終了までの期間であり、『〇日間』という一定の期間で表されます。商品の納期が1週間後だとしても、在庫があれば即日出荷できる場合、リードタイムは1日程度になります。
リードタイムは企業の内部プロセスを反映し、納期は顧客との契約上の期日を示すともいえるでしょう。製造業の場合、効率的な生産・配送システムを構築することで、リードタイムを短縮し、より柔軟な納期設定が可能になります。
■主な計算方法は2つ
リードタイムの計算方法には、『フォワード方式』『バックワード方式』の2種類があります。
フォワード方式は、作業開始日から各工程の所要日数を積み上げて、全体の日数を算出する方法です。着手日を早められるため、納期を急ぐ製造などに適しています。
一方、バックワード方式は完了日から逆算し、各工程の所要時間を割り当てる方法です。各工程の重複を避けながら、納期に合わせて着手時期を決定する際に使われます。
どちらの方式も、休業日を除いた営業日で計算するのが一般的です。状況に応じて適切な方式を選択することで、効率的なリードタイム管理が可能になります。
リードタイムを短縮するメリットとデメリット
リードタイムの短縮は、企業にとって多くのメリットをもたらします。一方で、現場を無視した大幅な短縮は、思わぬトラブルを引き起こします。以下、リードタイムを短縮するメリットとデメリットを理解しましょう。
■【メリット】コスト削減と収益力の向上
リードタイム短縮は、企業の収益力向上に直結します。受注からキャッシュ受け取りまでの期間が短縮されるため、キャッシュフローの安定化が期待できるでしょう。
製造業のリードタイムが長い場合、倉庫内の在庫が増えていき、在庫管理コストが増大します。リードタイムが短縮できれば、必要なときに必要な量だけを調達・生産できるため、保管スペースや管理人員、作業時間といったコストを抑えられるでしょう。
新たな事業に投資したり、既存の事業を拡大したりと、企業は資金を効率的に運用できるようになります。
■【メリット】競争力が強化される
リードタイムの短縮で迅速な製品提供が可能になると、顧客満足度が向上します。他社との差別化が可能になり、企業の競争力が強化されるのがメリットです。
例えば、ECサイトでは『当日発送』『翌日配達』といったスピーディーな対応が、顧客の購買意欲を高めます。スピードを求める現代、短納期化ができる企業は多くの顧客を引き付けるでしょう。
業界に先駆けてリードタイム短縮の仕組みを確立できれば、そのノウハウを生かした新たなビジネスチャンスの創出も期待できます。
■【デメリット】品質の低下につながる恐れがある
十分な体制を整備せずにリードタイム短縮を推し進めると、現場に大きな負担がかかります。「早く完成させなければ…」という焦りの気持ちから、現場では手抜き・ミスが多発する可能性もあるでしょう。
いくら短納期化が可能でも、商品・サービスの質が低下しては元も子もありません。場合によっては、顧客の安全に関わる重大なトラブルに発展する恐れもあります。現場に過度の負荷がかからないように、十分なコミュニケーションを取ることが肝心です。
リードタイムを短縮する取り組み例
リードタイムの短縮は、企業の競争力向上や顧客満足度の改善に不可欠です。ここでは、効果的なリードタイム短縮のための、具体的な取り組み例を紹介します。
■業務フローの見直し
業務フローの見直しは、リードタイム短縮の効果的な方法です。製造業を例に挙げると、以下のような改善ができます。
- 生産計画の見直し
- 業務フローの標準化
- 小ロット生産や工程の同期化
- 段取りの改善
- 設備レイアウトの見直しによる運搬時間の削減
- 5S(整理・整頓・清掃・清潔・しつけ)の徹底
ただし、小ロット生産は欠品リスクに注意が必要です。自然災害の発生や部品の仕入れ先の営業停止によって、生産をストップせざるを得ない場合、在庫分だけではサービス提供を賄えなくなる可能性があります。
■デジタル技術の活用
デジタル技術の活用は、リードタイム短縮に大きな効果をもたらします。例えば、3Dモデルを活用した設計・製造性の検証システムは、実機試作の削減や手戻り設計の軽減、工程設計の効率化などに貢献します。
部品管理(BOM)システムを導入すれば、人的ミスの軽減や情報共有の円滑化により、生産性が向上するでしょう。IoTやAIなどの最新技術を活用し、コスト削減や業務フローの改善を行う企業も少なくありません。
技術導入と並行して、部門間の連携強化や情報基盤の構築に取り組むことで、リードタイムの大幅な短縮が可能となります。
■最適な人員配置
リードタイムの短縮は重要ですが、現場に大幅な負荷がかかると、品質の低下や予期せぬトラブルが多くなります。現場の意見を取り入れながら、無理のない人員配置や工程改善を進めましょう。
例えば、作業が滞りやすいボトルネック工程においては、スタッフの増員や再配置を通じて、業務スピードを改善します。
また、スキルアップを目的とした研修・トレーニングを行うなど、スタッフの知識と技術力を底上げする施策も欠かせません。継続的な教育によって、リードタイムの短縮と品質の維持の両立が実現します。