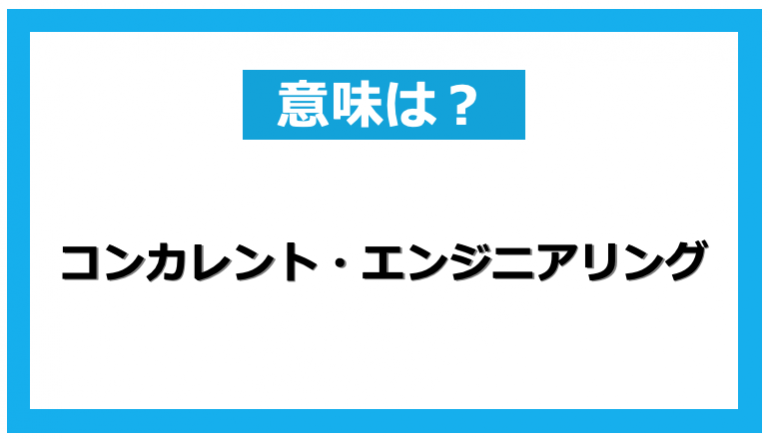
主に生産技術の分野で用いられる「コンカレント・エンジニアリング」という言葉をご存知だろうか。これは事業展開のスピードがビジネス成功のカギを握る今日、さまざまな分野で活用されている’’開発期間短縮の手法’’のことだ。
本記事では、コンカレント・エンジニアリングの意味や仕組みについてわかりやすく解説する。ぜひ、この機会に基礎的な概念を理解してほしい。
コンカレント・エンジニアリングとは?
「コンカレント・エンジニアリング:concurrent engineering」とは、開発プロセス短縮化の手法のこと。業務効率化によるコスト削減も期待できることから、多くの企業が取り入れている。
設計と生産性の検討を同時に進める手法
コンカレント・エンジニアリングは、1980年代に自動車製造の分野で提唱された概念。製造過程における企画・設計などの「上流工程」と、製造・テストなどの「下流工程」を同時並行で進めることで、開発に要する期間を短縮する手法を指す。主に製造業で活用される概念だが、建築分野などで応用されることも多い。
ソフトウェア開発分野などで注目されている「アジャイル開発」や「リーンソフトウェア開発」は、コンカレント・エンジニアリングの理念をもとに考案されたと言われている。
従来型開発手法との違い
従来まで製造業における開発工程は、「ウォーターフォール型開発」が主流となっていた。ウォーターフォール型開発は、その名の通り水の流れのように上流工程から下流工程に開発を進めていく手法。段階的に開発を進めていくため、全工程を完了させるまでにある程度の時間を要する。
これに対し、コンカレント・エンジニアリングは企画・設計・実装・テストの各ステップを同時並行で実施するため、開発期間の短縮が可能となる。
コンカレント・エンジニアリング導入のメリット
コンカレント・エンジニアリングを導入することで、開発プロセスの効率化を図ることができる。開発の初期段階から関連部門が集合し、作業を前倒し的に読み込む「フロントローディング」により、時間的・物理的ロスの削減が可能。また、製造や品質管理などの下流工程を含めた検討は、製品のクオリティ向上にも効果がある。
コンカレント・エンジニアリング導入のデメリット
メリットの多いコンカレント・エンジニアリングだが、導入体制の整備が不十分な場合、かえって開発プロセスを停滞させてしまうおそれがある。各部門が同時並行で開発を行う特性上、情報共有やコミュニケーションといった「ソフト面」の環境整備が肝要。
フロントローディングは設計部門への負荷が大きいため、設計士やオペレーターの人員配置などに配慮することもポイントだ。
コンカレント・エンジニアリングで用いられる2つの手法
開発の初期段階において工程上の問題点を発見・解決することがコンカレント・エンジニアリングを導入する目的の一つ。この問題発見と解決に活用される手法が「イレギュラーチェックリスト」と「逆レジデント・エンジニア」。ここでは、それぞれの概要を解説する。
イレギュラーチェックリスト
イレギュラーチェックリストとは、製造における生産・運用・提供の各段階で、イレギュラーとなる事象や問題点を共有するためのツール。比較的早期の段階で品質やコストに影響を与えるリスクを発見することができるため、適切かつ効果的な改善策を投じることが可能となる。
逆レジデント・エンジニア
逆レジデント・エンジニアとは、商品の設計段階に技術や販売、運用などの部門スタッフが乗り込んでいく手法。計画の初期段階において他部門のノウハウを参考にできるため、品質向上やコスト削減に大きく貢献する。
コンカレント・エンジニアリングに必要なITツール
最後に、コンカレント・エンジニアリングに欠かせないITツールを紹介する。ここで紹介するシステムは、企業の「コンカレント化」において重要な役割を果たしている。
CAD(Computer Aided Design)
CAD(Computer Aided Design)は、製品設計や図面の作成をコンピューター上で行うためのツールで、日本語では「コンピューター支援設計」と訳される。CADを活用することで、製品の設計作業を効率的に行うことが可能。現在では、3Dモデルを設計する「3D CAD」も存在する。
CAM(Computer Aided Manufacturing)
CAM(Computer Aided Manufacturing)とは、コンピューター上で生産工程の管理や制御を行うためのシステムで、日本語では「コンピューター支援生産」と訳される。図面の情報を工作機械用の言語に変換するツールで、CADと組み合わせて活用されることが多い。
CAE(Computer Aided Engineering)
CAE(Computer Aided Engineering)は、製造過程における数値の解析やシミュレーションを行うためのシステム。CADで作成したデータをCAEで読み込むことで、コンピューター上での製品テストが可能となる。日本語では「コンピューター支援解析システム」と訳される。
PDM(Product Data Management)
PDM(Product Data Management)とは、設計管理に関するデータを一元管理するためのツールで「製品情報管理システム」とも言われる。PDM を活用することで、CADで作成した設計データやBOM(部品表)など、製品に関連する情報をまとめて管理することが可能。情報共有に欠かせないシステムだ。
文/oki