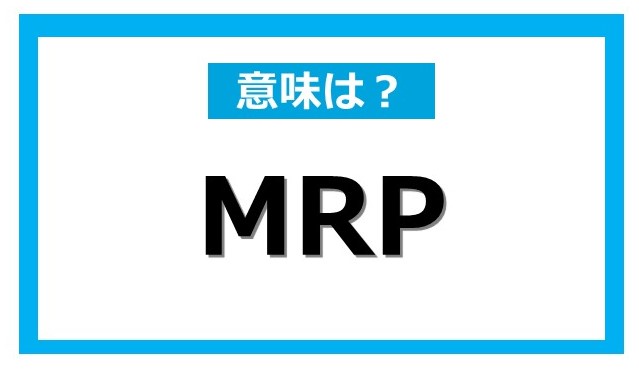
『MRP』は生産管理に用いられる手法の一つです。物や人、設備など、製品を製造する際に必要なあらゆる事柄に対して、効率的な働きを促すために使用されます。具体的な中身や導入の目的、運営方法などを詳しく紹介します。
生産管理における「MRP」の意味とは?
製造業において、現場を効率化し生産性を向上させることはビジネス上の課題の一つです。これらを解決に導く手法として注目される『MRP』について解説します。
資材所要計画のこと
「MRP」は、『Material(素材)』『Requirements(要求・必要条件)』『Planning(計画)』の頭文字をとって作られた言葉で、日本語では『資材所要計画』と訳されます。
1970年代初頭に『アメリカ生産在庫管理協会(APICS)』が提唱し、70年代後半から日本でも導入され始めました。
生産性の向上を目指すための生産管理方式で、一つの商品を製造するために『必要なものを』『必要なときに』『必要なだけ』調達する方法です。
一般的に、製品を完成させるまでには下記のようなさまざまな工程を経る必要があります。
- 資材の調達
- 作業場所の確保
- 製造に必要な設備の整備
- 作業員の配置
- 作業工程の計画立案と管理
- 納期から逆算した作業日程の設定
これらを効率的に実行・管理していくために立てられるのが『生産計画』で、大手企業などでは生産計画の実行や管理を専門に行う『生産管理部門』が設置されています。
生産管理においてMRPとITを活用することで、よりスマートな運営を行う企業が増えています。
MRPの必要性
生産現場でMRPを導入する必要性は、大きく分けて以下の三つがあります。
- エラーの予防になる
- 人手不足の解消につながる
- 在庫を減らせる
近年の製造業は、多品種・少量生産が主流で作業工程が複雑化しています。
そのため、MRPを導入することで、複雑な工程の中で起こりうる人的な計算ミスや発注ミスといったエラーを未然に防ぎます。
また、近年の製造業では人手不足が深刻化しています。
MRPを導入して生産管理作業をITで自動化することで、生産管理に割いていた人的リソースが削減できれば、不足している部門や適した部門に人材を配置することが可能です。
さらに、MRPの導入で資材の調達や管理が最適化されれば、必要以上に在庫を抱える必要がなくなり、無駄を省くこともできるのです。
MRPのメリット
ここまで、MRPの概要について説明してきました。次に、MRPを導入する具体的なメリットについて、詳しく解説していきます。
生産の効率化を図れる
MRPの導入により『製造に必要な資材の量』や『納入時期の最適化』が実現できれば、全体的な生産の効率を高められます。
計画的に生産を行うことで、『資材の在庫不足で生産ラインがストップし、その分を補うために工程を入れ替える』といった余分な作業がなくなるでしょう。
製造の現場で生産の効率化が実現できれば、納期の厳守や品質の維持などにもつながり、ひいては会社全体の『QCD(品質・コスト・納期)』の向上も期待できます。
無駄の削減につながる
MRPにより計画的な資材の購入が実現されると、無駄な資材発注がなくなり、資材調達に関わるコストが削減できます。
製造にかかる不要なコストを削減することで、結果として製品価格も下げられるでしょう。そうやって製品を競合他社より安く提供できれば、企業の市場競争力が向上します。
さらに、MRPの導入で生産管理での工数も省けるため、生産管理にかかる労働力や人件費の削減も可能です。
サービスが向上する
MRPを導入することで、市場や顧客へのサービスの向上が図れます。具体的には、下記のような内容が挙げられます。
- 納期を守って納品し、予定通りに製品を市場に提供できる
- 在庫切れが起こりにくく、消費者に求められたらすばやく対応できる
- 常に一定の生産体制を維持できるため、製品の品質を落とさずに済む
このように、消費者が求める品を、求められるときに・求められた分だけ・的確に提供できる状態は、顧客サービスの向上にもつながるのです。
MRPの流れを分かりやすく!
MRPは、資材調達から納品までの長い工程を管理する手法です。実際にMRPを行う場合には、次のような流れで生産の最適化を進めます。
情報から予測を立てる
まずは、過去の実績や今後の販売計画といった情報から製品の需要予測を立て、製造する個数の見積もりを出します。
販売統計や季節変動など、さまざまな方面のデータを分析し、いつ・どこに・どんな商品が・どのくらい必要なのかを予測します。
企業においてこの工程を担当するのは、主に営業部門です。
生産計画を作成する
まとめられた需要予測をもとに行われるのが、詳細な生産計画の作成です。この生産計画は、『MPS(マスタープロダクションスケジュール)』とも呼ばれます。
既存の製品であれば、企業は在庫を抱えている場合がほとんどです。そのため、既存の製品を扱う場合は、企業が抱えている在庫の状況も計算に入れた上で、生産計画を立てていきます。
必要数を計算して発注する
生産計画を立てて製造する個数を確定させたら、その個数を作るのに必要な部品を発注します。
一つの製品を作るのに必要な資材一覧を、部品表(BOM)といいます。生産計画により弾き出された製造する個数と在庫数、BOM を照らし合わせ、調達すべき資材の種類と必要量を算出するのです。
さらに、発注から納品までにかかる時間や資材を保管する倉庫の状況なども加味した上で納期を決定し、資材を発注します。
MRPを導入する際のポイント
MRPによる効果を最大限に生かすためには、導入する際にいくつかのポイントがあります。ここでは、その中から二つのポイントについてみていきましょう。
BOMで在庫を明確にする
製品を作るのに必要な資材を一覧にしたものを、『部品表(BOM)』と呼びます。
MRPを効果的に導入するには、BOMを正確に作成し、在庫と照らし合わせて『どの部品が・あとどれだけ必要か』を算出することが重要です。
必要な部品が漏れていたり、個数が間違ったりしているBOMを使ってMRPを立ててしまうと、製造の途中で部品不足が起こって製造ラインが止まったり、必要以上の無駄な資材を発注したりと、生産性や効率性を高めることができなくなります。
MRPに必要不可欠なBOMですが、「作成したことがない」「必要としてこなかった」という企業もあるでしょう。
製造においてIT化が進むにあたり、BOMはいずれ必要となります。MRPの作成をコンピューターが行う場合でも、計算に必要なデータ(BOMの情報)は人の手でインプットしなければならないからです。
そのため、時間と労力をかけてでもBOMは作り込んでおくことが大切です。
情報共有が大切
MRPを効果的に進めていくためには、MRPの元で動く全ての部門で、タイムラグのない情報共有ができる体制を整える必要があります。
生産ラインは、ある意味『生き物』です。毎日、MRP通りに製造工程が進んでいけば問題ありませんが、そのように進む可能性は非常に低いのが現実です。
『納期に資材の搬入が間に合わない』『天候不良で流通に支障が出た』『製品の欠陥が見つかった』などのハプニングが起こったり、製品の仕様変更や計画変更、発注数の変更といった事態が起こったりすることはよくあります。
それら全てに臨機応変に対応するためには、MRPによる生産計画自体も、現場の状況の変化に合わせて定期的にアップデートする必要があるのです。
構成/編集部